Continuous Process Improvement
No matter where you are in your continous improvement or lean manufactruing journey, OnTakt can help ensure your success. OnTakt enables the successful implementation of a wide variety of lean methodology tools to streamline your operations.
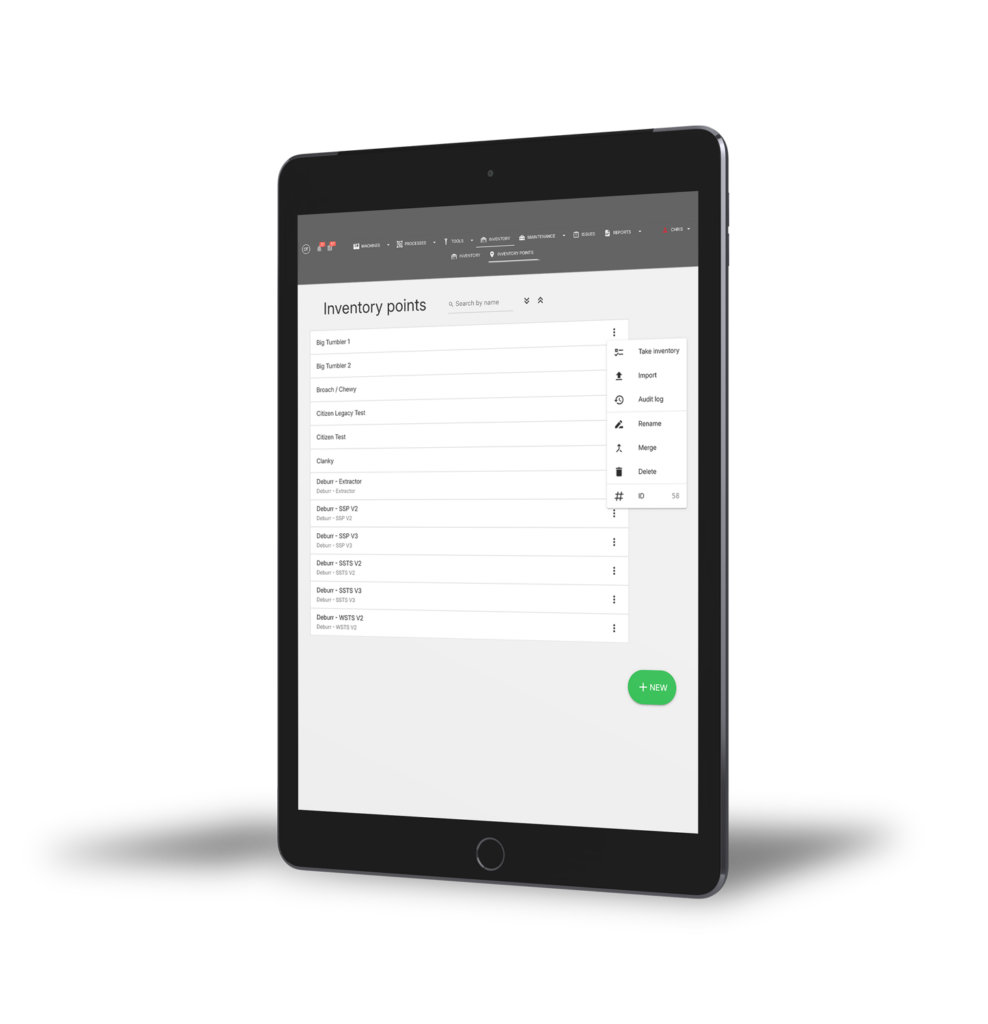
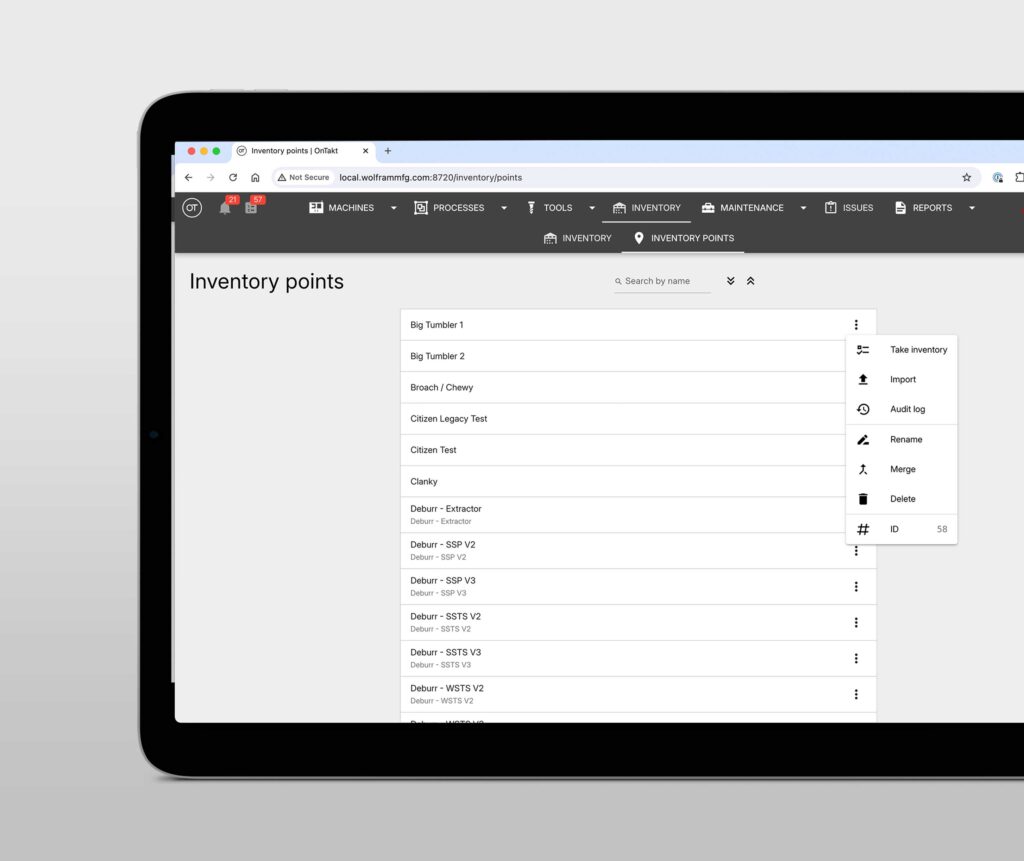
5S
OnTakt can help you organize your shop workspaces with 5S by clearly providing inventory points for shop supplies, consumables, and more. The Inventory module in OnTakt allows you to create custom inventory locations to suit your workspace.
Kaizen
OnTakt is an excellent resource for your team to run Kaizen events at your manufacturing facility.
OnTakt’s Downtime and Issues features can help you:
- Identify problem areas in your shop and provide you with a dollar value of what the issue is costing you
- Observe through the collection and recording of data prior to your Kaizen event to set a baseline
- Target areas to test, evaluate, and validate potential improvements
- Record data after the implentation of the improvements to prove the value of the improvements
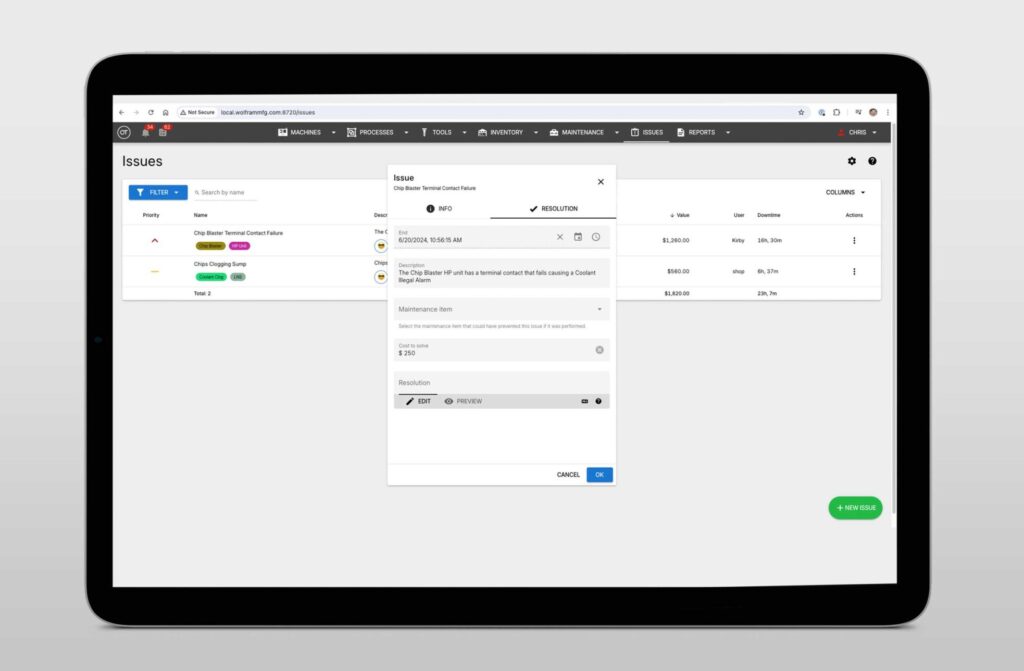
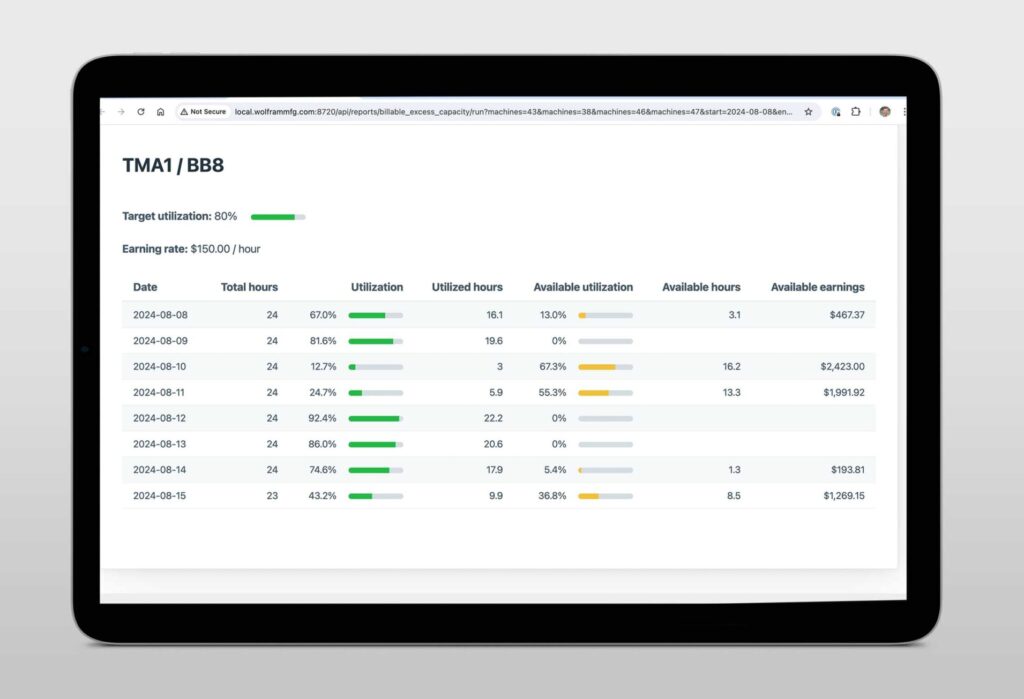
SMED
When it comes to CNC machining, optimizing machine setup times is crucial, as it can significantly impact the profitability of a job. By collecting state utilization data of your machines, you can identify opportunities to improve your setup processes.
Additionally, by tracking the cost of downtime due to setup (through reports like the Billable Excess Capcity Report) you can identify the cost in dollars of set up time. This allows your improvement team to have a clear ROI for setup improvements and can help justify the addition of quick change tooling, pallet systems, and robotic load/unload systems.
Value Stream Mapping (VSM)
OnTakt can help you create a value stream map from scratch or hone an existing value stream map by tracking the cycle times of parts you make in your shop. You can analzye cycle times over different time periods (such 1st shift vs. 3rd shift) to identify waste and increase efficiency.
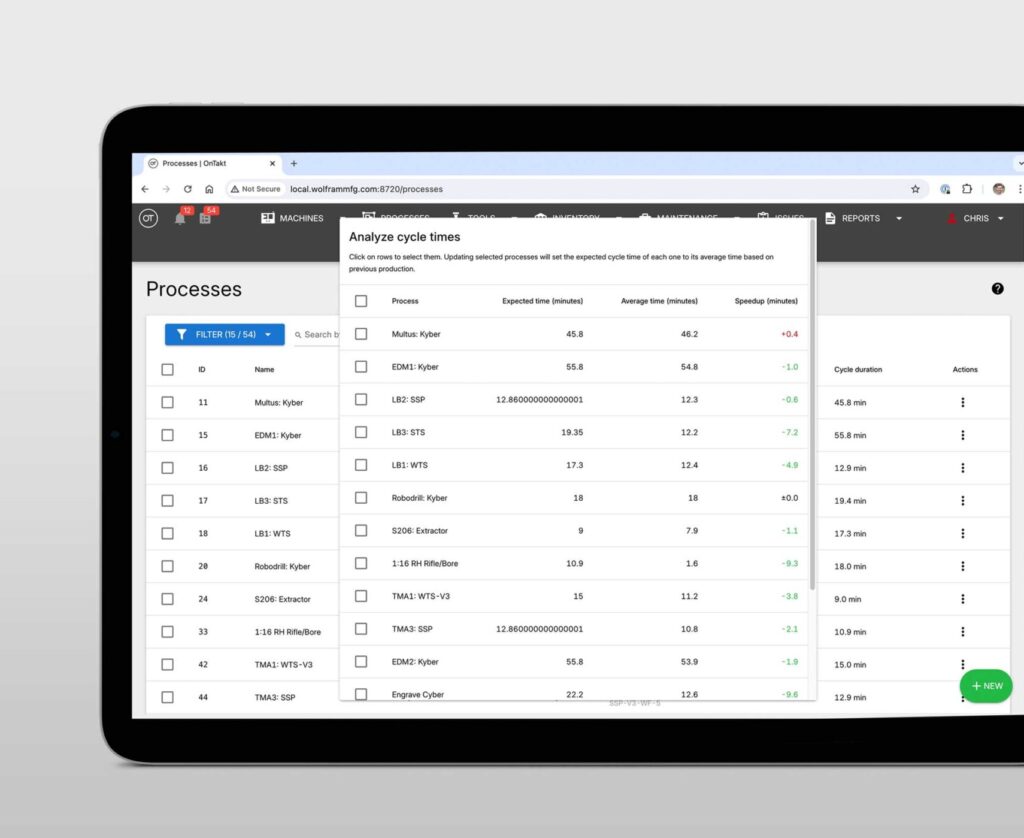
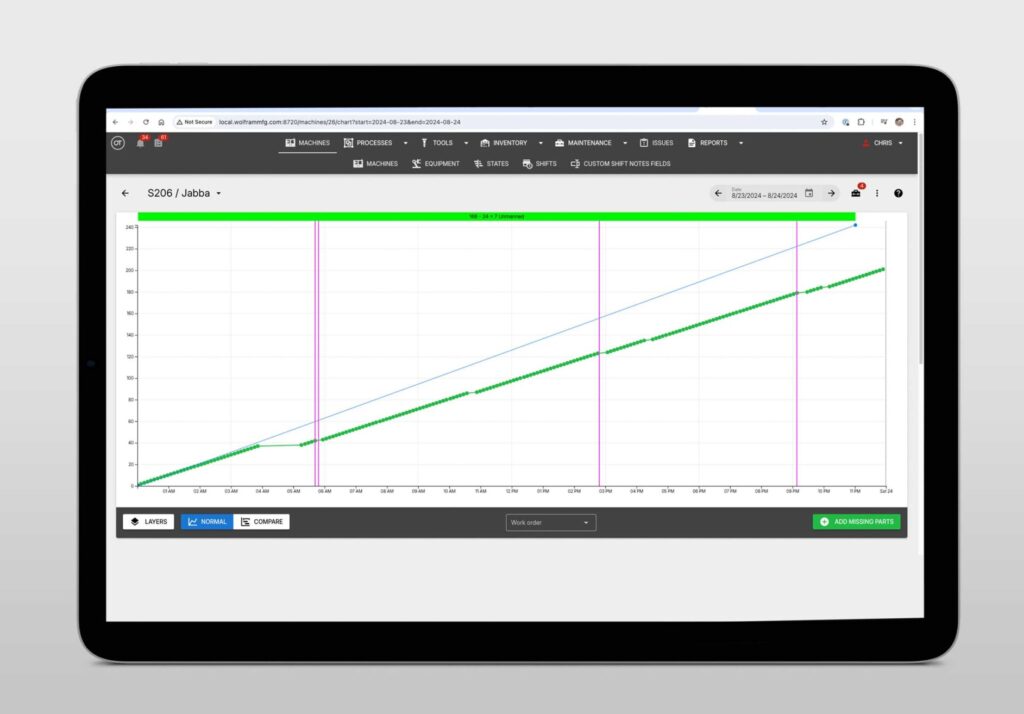
Bottleneck Analysis
OnTakt can help you identify the areas of your process that are creating bottlenecks. With the ability to set production targets and know minute-by-minute where your production is in comparison to your production target, you can immediately identify bottlenecks before they become a problem. Additionally, ongoing bottlenecks can be tracked through part cycle times as well as the Issues module to streamline your processes.
Root Cause Analysis
Macro variables in your control can be used to take inspection data and component serial numbers to further enhance the data capture and traceability that can help you with root cause analysis on the shop floor.
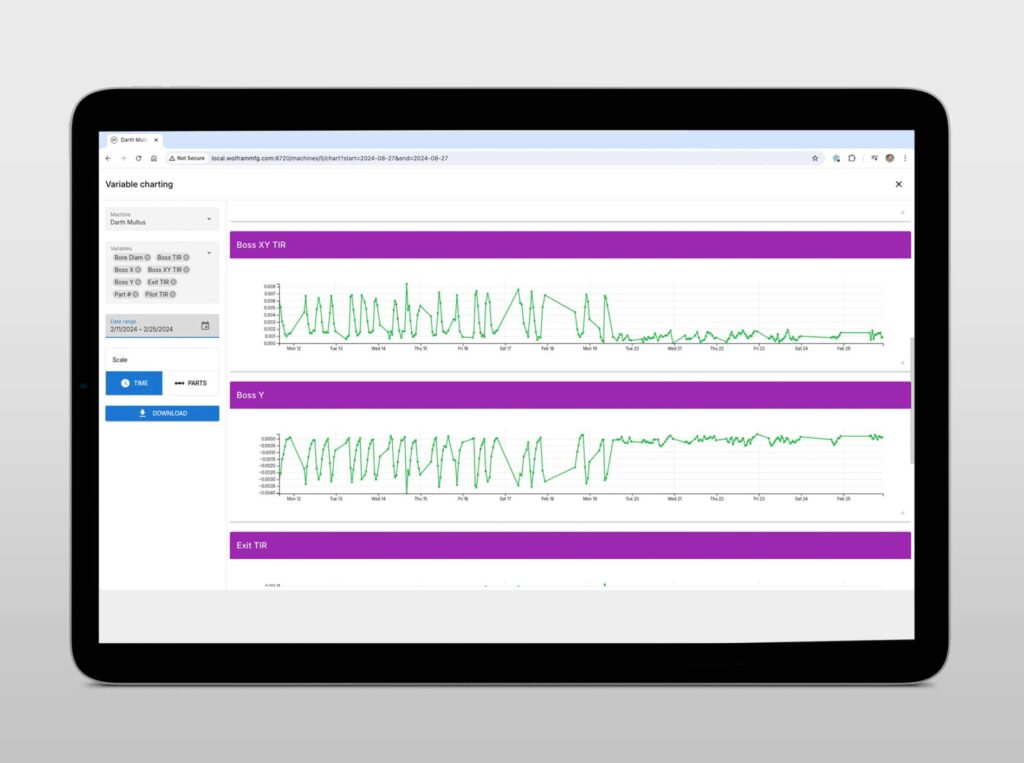
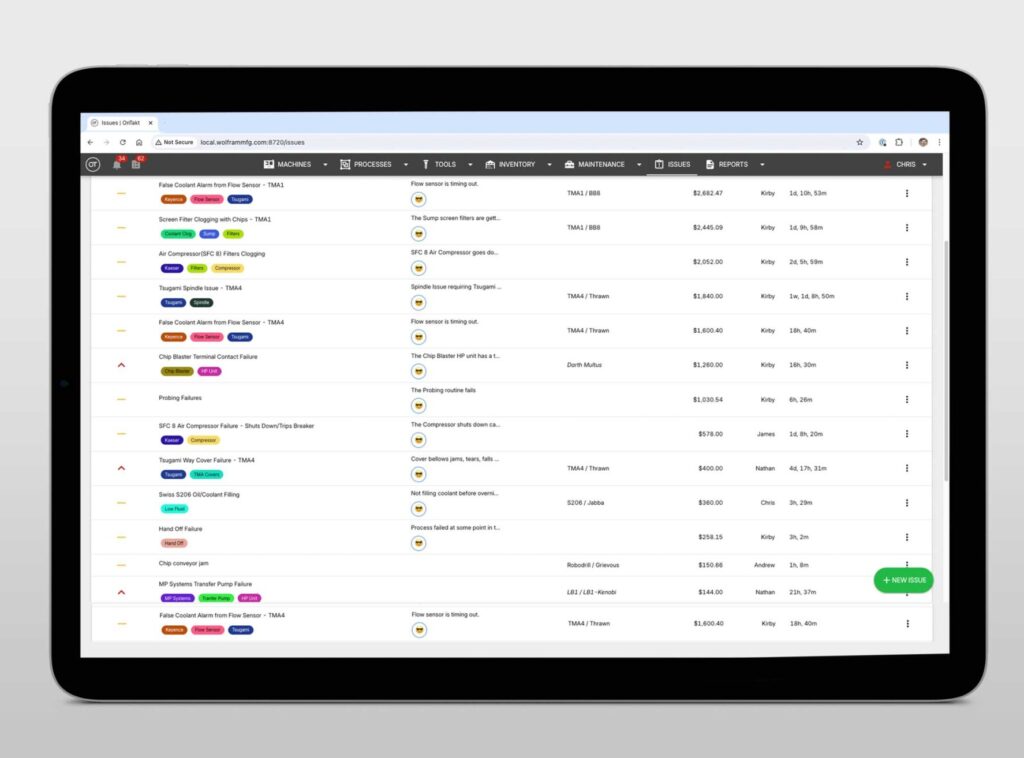
Six Sigma
OnTakt can help your six sigma program with every element of the DMAIC methodology. Across the OnTakt modules we can help you Define, Measure, Analyze, Improve and Control processes on your manufacturing floor.
Ready to get started?
Find out how OnTakt enables machine shops of all sizes to easily leverage data to increase productivity and profitability.